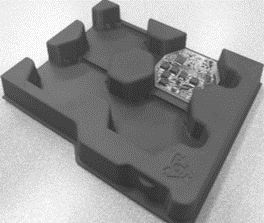
Problèmes identifiés :
- Nombreuses récursions d’outillage nécessaires pour aboutir à un conditionnement produit conforme (détermination du jeu fonctionnel, risques qualité liés aux mouvements possibles des produits dans les alvéoles, détermination des cotes d’empilement, validation du passage des blisters sur ligne de fabrication avec empileurs / dépileurs…)
- Temps d’approvisionnement des blisters définitifs trop long et trop onéreux.
Solution :
- Impression 3D de blisters pour tests en conditions.
- Adaptations et récursions 3D en temps réel.
- Validation de la géométrie avant lancement en production « traditionnelle »
Gains :
- Raccourcissement du calendrier de production (70%)
- Réduction des coûts d’outillage (50%) et du temps de traitement administratif (passage de commandes)
- Utilisation exclusive de blisters imprimés en 3D pour certaines petites productions (plus de coûts outillage)
- Démonstration d’agilité au client.
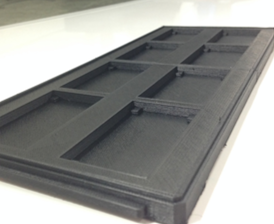